Precise, safe and efficient: the navigation of our automated guided vehicles (AGVs) is the basis for a smooth material flow in automated intralogistics. By precisely determining the position and destination, our transport robots control their direction and speed in real time – even in complex or dynamic environments. The result: maximum process reliability, flexibility and efficiency in your intralogistics.
![[Translate to Englisch:] [Translate to Englisch:]](/fileadmin/_processed_/b/7/csm_ek-robotics-navigation-lp-01_5beb68d806.jpg)
Intelligent navigation for every environment
We use reflector or contour navigation for the navigation of our automated guided vehicles – adapted to the respective environment. In special applications such as block storage, magnetic point navigation complements the system. All types of navigation can be flexibly combined into a hybrid solution to ensure maximum precision and adaptability. CAD-based route planning enables easy implementation of even complex route networks.
Advantages of hybrid laser navigation at a glance
Minimal installation effort
Reflectors are only needed where no environment-based navigation is possible – this saves time and costs.
Maximum navigation reliability
The vehicle position is checked every 50 milliseconds – for maximum reliability during operation.
Automatic position detection
After manual interventions, the vehicles can find their way around independently – no manual reset is necessary.
Flexible layout design
Driving courses can be easily adapted using CAD – ideal for dynamic production environments.
High precision and speed
Positioning with an accuracy of ±10 mm and driving speeds of up to 2 m/s ensure maximum efficiency.
Less hardware, more range
High-performance laser scanners with a range of up to 70 m reduce the use of reflectors to a minimum.
Do you have questions?
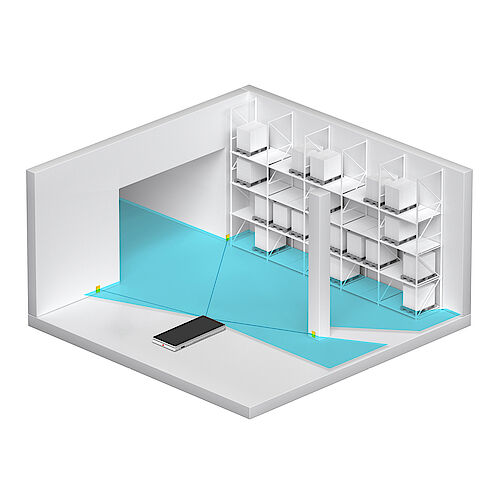